Enhancing Your Business with MTU Spares Order Solutions
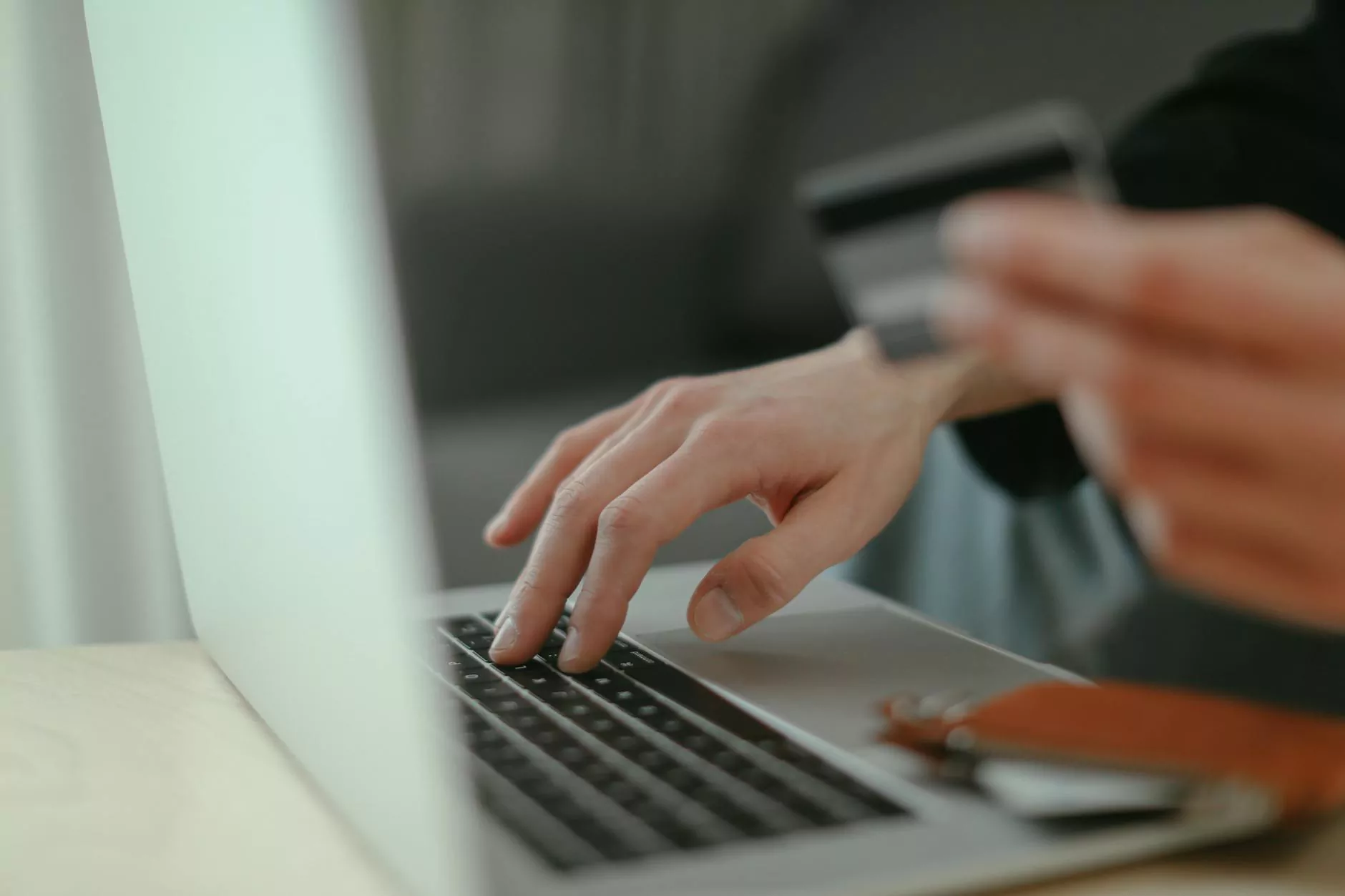
In today's highly competitive market, every business must strive for efficiency, cost-effectiveness, and quality. For companies involved in diesel engine manufacturing and generator supply, an essential component of maintaining these standards is a streamlined spares order process. In this article, we will discuss the significant impacts of MTU spares order solutions on your business operations, enhancing performance, supporting sustainability, and driving profitability.
Understanding MTU Spares Order
MTU, a prominent name in the diesel engine industry, is revered for its reliable and durable engines. When we refer to an MTU spares order, we mean the procurement of genuine, high-quality spare parts—critical for the maintenance and longevity of your diesel engines and generators.
The Importance of Using Genuine Spare Parts
When it comes to engine parts, using genuine MTU spares is vital. Here are several reasons why:
- Quality Assurance: Genuine parts guarantee high quality and performance.
- Durability: They help ensure the longevity of your engines and generators.
- Efficiency: Properly fitting parts optimize the operational efficiency of machinery.
- Warranty Protection: Using genuine parts protects your warranty agreements.
- Environmental Compliance: Genuine parts are often designed with sustainability in mind.
How to Streamline Your MTU Spares Order Process
Streamlining your MTU spares order process not only saves time but also reduces costs. Here are several strategies that can help:
1. Develop a Comprehensive Inventory Management System
Implementing an effective inventory management system ensures that you always have the required spare parts at hand. This system should allow you to:
- Track Inventory Levels: Monitor your stock levels to avoid shortages.
- Forecast Demand: Analyze trends to predict future spare parts needs.
- Automate Reorders: Set automated reorders for frequently used parts.
2. Utilize Technology for Order Management
Integrating ordering systems such as ERP (Enterprise Resource Planning) software can significantly streamline your MTU spares order process. Consider the following:
- Centralized Database: Maintain a centralized database for all orders and inventory.
- Mobile Access: Allow your team to place orders and view inventory from any location.
- Supplier Integration: Facilitating easy communication with suppliers for swift reordering.
3. Partner with Reliable Suppliers
Establishing relationships with dedicated suppliers of MTU parts is key. Choose suppliers who:
- Understand Your Business Needs: Know what you require to ensure minimal downtime.
- Provide Timely Deliveries: Reliability in delivery schedules is essential.
- Offer Competitive Pricing: Ensure you get value for your money while maintaining quality.
Benefits of Optimizing Your MTU Spares Order Process
Implementing a robust MTU spares order strategy results in multiple benefits that will transform your business. Below, we discuss these advantages:
1. Increased Operational Efficiency
An optimized order process leads to faster turnaround times, enabling your business to respond quickly to client needs and project demands. This efficiency contributes directly to increased customer satisfaction.
2. Cost Reduction
By managing your spares effectively, you will minimize the costs associated with emergency purchases and downtime, maximizing your overall profitability.
3. Improved Compliance and Risk Management
Maintaining a steady supply of genuine MTU parts ensures your engines comply with regulations, reducing legal risks and enhancing corporate social responsibility (CSR).
4. Enhanced Reputation
Companies known for their quality operations often enjoy a solid reputation. By utilizing genuine spare parts and streamlining your order process, you reinforce your brand’s commitment to quality and sustainability.
Real-Life Examples of Successful MTU Spares Order Implementation
Numerous businesses have successfully implemented MTU spares order optimization strategies. Let’s take a look at some case studies:
Case Study 1: Global Diesel Manufacturer
A global diesel engine manufacturer faced challenges with parts availability, resulting in project delays. By investing in a modern inventory management system and establishing partnerships with qualified suppliers, the company reduced its parts lead times by 40%. This transformation significantly improved their project delivery timelines and client satisfaction.
Case Study 2: Diesel Generator Supplier
A diesel generator supplier implemented automated ordering processes integrated with their supplier's system. This approach allowed for real-time inventory tracking and increased order accuracy. As a result, the supplier reported a 30% increase in overall operational efficiency and a substantial drop in costs associated with overstocking and stockouts.
Guidelines for Future MTU Spares Order Practices
To ensure continued success with your MTU spares order, consider the following guidelines:
- Regularly Review Supplier Performance: Build long-term relationships with your suppliers while assessing their performance periodically.
- Embrace Technology Innovations: Stay updated with the latest inventory and order management technologies.
- Continue Staff Training: Ensure your team is trained in efficient order management practices.
Conclusion
In conclusion, a well-managed MTU spares order process not only enhances operational efficiency but also plays a crucial role in driving customer satisfaction and business success. By focusing on quality, technology, and strong supplier relationships, businesses in the diesel engine manufacturing and generator supply industry can attain superior performance and a competitive edge. Start today, and witness the transformation in your operational capabilities!
For more information on optimizing your diesel engine operations through effective spares ordering, visit engine-family.com.