Unlocking the World of Screenprinting Materials
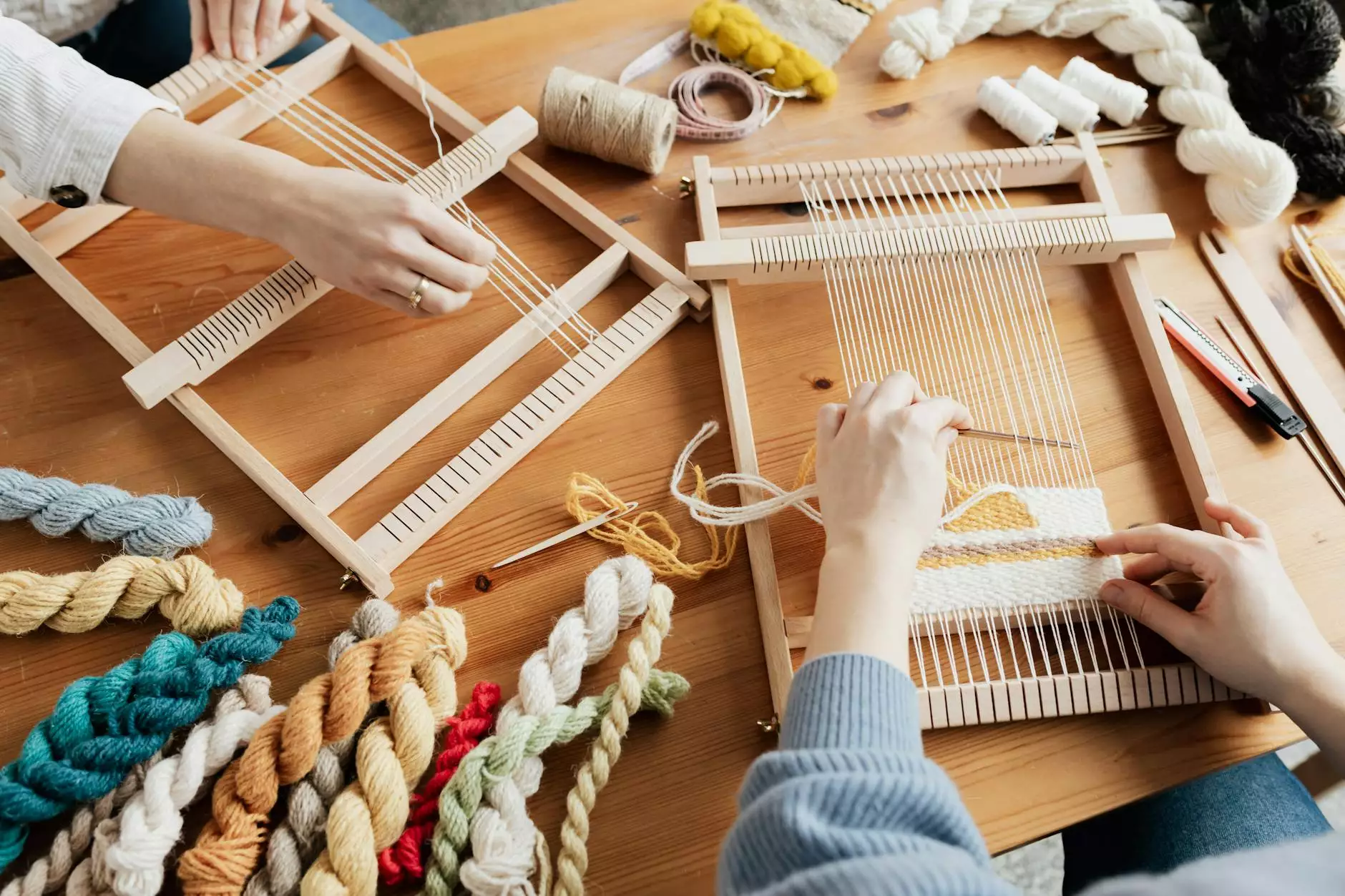
Screen printing is an age-old technique that has evolved into a sophisticated and efficient medium for creating vibrant and durable prints. Understanding screenprinting materials is crucial for anyone looking to excel in this craft, whether for personal projects or industrial applications. In this extensive guide, we will explore the various types of materials used in screen printing, their unique properties, and how to choose the right ones for your specific needs.
What is Screen Printing?
Screen printing, also known as silkscreen printing, is a method where designs are transferred onto a substrate (such as fabric, paper, or plastic) through a mesh screen. The areas of the screen that are not part of the design are blocked, allowing ink to pass through only the desired portions. This technique allows for bold colors and intricate designs that last longer than many other printing methods.
The Importance of Choosing the Right Screenprinting Materials
Choosing the right materials is paramount for the success of your screen printing projects. The materials can greatly affect the quality, durability, and vibrancy of your prints. By understanding the different types of materials available, you can make informed decisions that enhance your work and meet your specific needs.
Types of Screenprinting Materials
Below is a comprehensive overview of the essential screenprinting materials commonly used in the process:
1. Mesh Screens
- Material Composition: Mesh screens are typically made from nylon or polyester.
- Mesh Count: The mesh count (number of threads per inch) determines the detail and thickness of the ink deposit. Common counts range from 110 to 305.
- Application: Lower counts are used for thicker inks on fabrics, while higher counts work well with fine details.
2. Emulsion
- Type: Photo emulsion is most commonly used for creating stencils on mesh screens.
- Application: After applying to the mesh and allowing it to dry, your image is exposed to light, hardening the emulsion in the pattern of your design.
- Benefits: Allows for high-resolution prints with crisp edges.
3. Inks
- Types: There are various types of inks used in screen printing, including plastisol, water-based, and discharge inks.
- Plastisol Inks: These inks do not dry unless heated, making them perfect for screen printing on fabrics.
- Water-Based Inks: Environmentally friendly and excellent for soft prints, suitable for lighter fabric colors.
- Discharge Inks: These inks bleach the dye out of fabric instead of sitting on top, resulting in a soft feel.
4. Squeegees
- Material: Typically made of rubber or polyurethane.
- Sizes & Shapes: Available in various sizes and durometers, suitable for different ink types and mesh counts.
- Application: Used to push ink through the mesh screen and onto the substrate.
5. Substrates
- Types: Common substrates for screen printing include fabrics (cotton, polyester), paper, glass, and plastics.
- Considerations: The type of substrate influences the selection of ink and mesh.
How to Choose the Best Screenprinting Materials
Selecting the right screenprinting materials can greatly enhance your print quality and efficiency. Here are some key factors to consider:
1. Desired Effect
Determine the visual and tactile effects you want to achieve. If you aim for a soft hand feel, consider using water-based or discharge inks. For vibrant and durable prints, plastisol may be the better choice.
2. Fabric Type
The type of fabric you are printing on will dictate your choice of inks and emulsions. For example:
- Cotton Fabrics: Can work well with all types of inks.
- Polyester Fabrics: Preferably use plastisol inks for better adhesion.
3. Print Design Complexity
If your design features fine details, opt for a higher mesh count and the appropriate type of emulsion. Conversely, for larger blocks of color, a lower mesh count will suffice.
4. Budget Considerations
High-quality screenprinting materials can vary significantly in price. Assess your budget to strike a balance between quality and cost. Investing in better materials often leads to superior results, reducing the likelihood of rework.
Essential Tips for Working with Screenprinting Materials
Here are some proven tips to optimize your use of screenprinting materials:
1. Proper storage
Ensure that all screenprinting materials are stored in a cool, dry place to maintain their longevity and effectiveness. Inks should be sealed properly, and emulsions should be stored away from direct light.
2. Consistent Mixing
When mixing inks, always ensure that they are mixed uniformly. This guarantees consistent color across multiple prints.
3. Test Prints
Before running a full production run, conduct test prints to troubleshoot any issues with design, ink thickness, or substrate compatibility.
4. Regular Maintenance
Keep screens, squeegees, and other tools clean to ensure optimal performance. Build-up can lead to inconsistent prints.
The Future of Screenprinting Materials
As technology evolves, so does the world of screenprinting materials. Innovations such as eco-friendly inks, advanced mesh technology, and automated printing processes continually reshape the industry. Introducing cutting-edge materials can improve efficiency and quality, catering to the green movement and heightened consumer preferences for sustainable products.
Conclusion
In the realm of screen printing, understanding and choosing the right screenprinting materials is integral to success. By familiarizing yourself with the various materials, their applications, and how to select the best options for your projects, you can elevate your screen printing endeavors to new heights. Whether you’re a seasoned printer or a newcomer, investing time in mastering these materials will undoubtedly pay off in the quality of your work. Explore the offerings of Boston Industrial Solutions to find everything you need for your screen printing journey.