High Precision Injection Molding: Transforming the Manufacturing Landscape
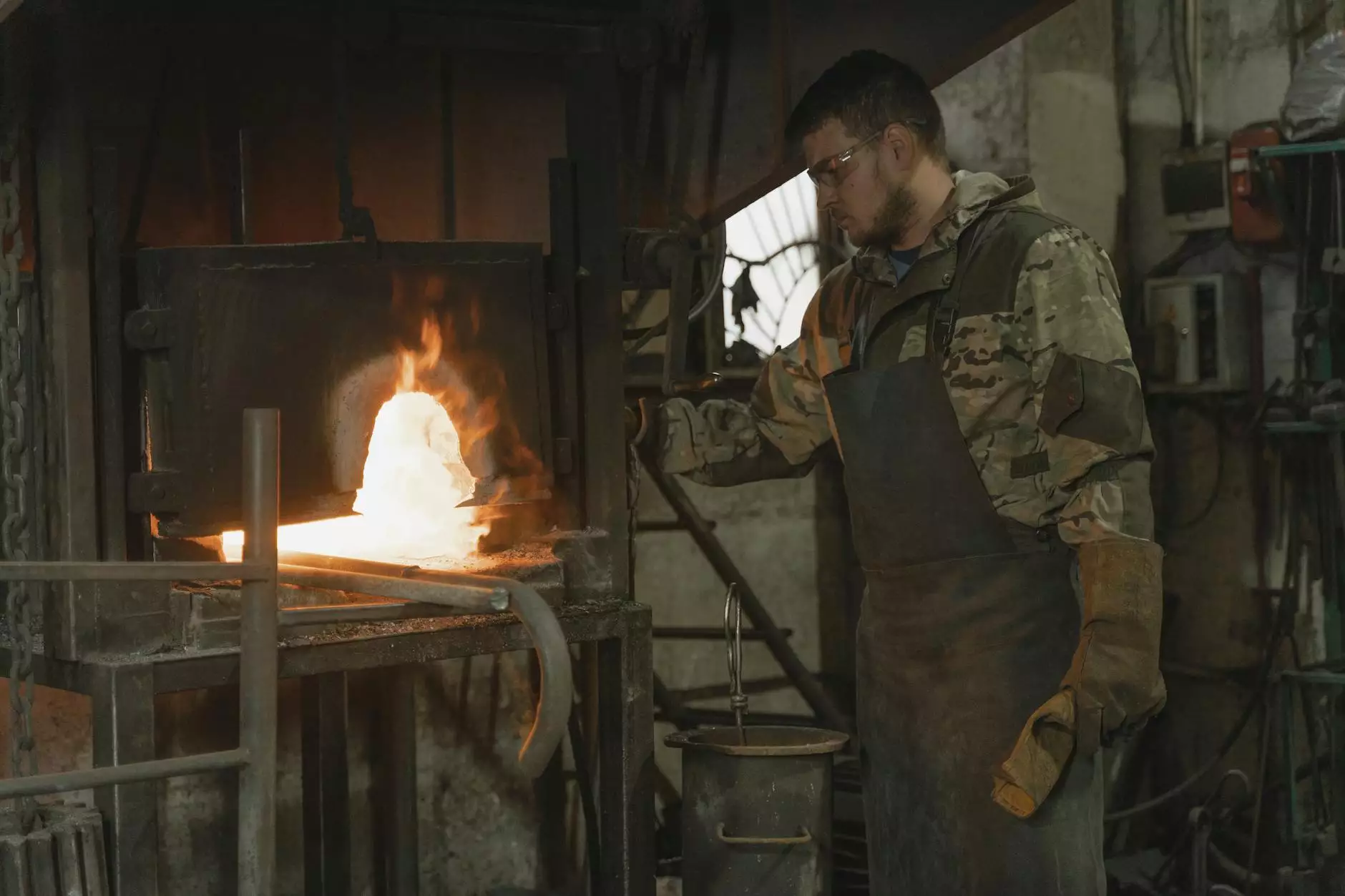
High precision injection molding has revolutionized the manufacturing landscape by enabling the production of complex shapes and detailed designs with exceptional accuracy. This advanced technology is widely used in various industries, including automotive, electronics, medical devices, and consumer products. Thanks to companies like DeepMould, the path to manufacturing excellence has never been clearer.
The Core of High Precision Injection Molding
At its core, high precision injection molding is a process that involves injecting molten material into a mold to create desired shapes. While the basic concept may not sound groundbreaking, the precision with which this process can be executed is what sets it apart. This section breaks down the essential aspects of this innovative manufacturing technique.
Understanding the Process
The process of high precision injection molding involves several key steps:
- Material Selection: The first step in the process is selecting the appropriate thermoplastic or thermosetting polymer. Common materials used include ABS, polycarbonate, and PVC.
- Heating the Material: The selected material is then heated until it reaches a molten state, which allows it to flow easily into the mold.
- Injection: The molten material is injected into a precisely designed mold cavity under high pressure. This step is crucial for achieving high accuracy in the final product.
- Cooling: Once the mold is filled, the material is allowed to cool, solidifying into the shape of the mold.
- Demolding: After cooling, the molded part is removed from the mold, ready for further finishing or assembly.
Benefits of High Precision Injection Molding
The advantages of adopting high precision injection molding are manifold. Here we dive into some of the most significant benefits:
- Consistency: High precision leads to consistent product quality, essential for mass production.
- Complex Geometries: The process allows manufacturing complex designs that would be difficult or impossible using other methods.
- Cost Efficiency: Though initial setup may require investment, the long-term savings from reduced waste and faster production times are undeniable.
- Material Versatility: A vast array of materials can be used, providing flexibility for manufacturers to choose the best fit for their applications.
- Less Post-Processing: Parts often require little to no machining, as they can be molded directly to the desired specifications.
Applications of High Precision Injection Molding
High precision injection molding is instrumental across a multitude of sectors. Here are several notable applications:
Automotive Industry
The automotive industry relies heavily on high precision injection molding for manufacturing various components, such as:
- Dials and knobs
- Engine parts
- Interior trims
- Exterior body parts
Consumer Electronics
In consumer electronics, precision is pivotal for components like:
- Phone casings
- Buttons and connectors
- Enclosures for sensitive devices
Medical Devices
Medical device manufacturing demands unmatched precision. High precision injection molding is used for:
- Syringes and drug delivery systems
- Diagnostic equipment housing
- Implants and prosthetics
Challenges in High Precision Injection Molding
Despite its numerous advantages, high precision injection molding is not devoid of challenges that manufacturers must navigate:
Tooling Costs
One of the significant investments involved in the process is the cost of creating injection molds. High-quality molds can be expensive, particularly for complex parts.
Material Limitations
While there are many materials available, each has its characteristics and limitations. Understanding these limitations is critical for manufacturers to avoid production downtime and quality issues.
Process Stability
Maintaining process stability through variables such as temperature and material viscosity is essential to ensure the quality of each product.
DeepMould: A Leader in High Precision Injection Molding
With the rise of high precision injection molding, companies like DeepMould have positioned themselves as leaders in the field. Their commitment to quality, innovation, and customer satisfaction makes them a top choice for businesses in need of metal fabrication solutions.
Innovative Techniques
DeepMould utilizes the latest techniques and technologies in the field, ensuring that clients receive components that meet the highest standards of precision. This includes:
- Advanced computer-aided design (CAD) for mold design
- Robust quality control measures throughout the production process
- Custom material selection based on product requirements
Sustainability Practices
In addition to technological advancements, DeepMould is committed to sustainable manufacturing practices. This includes:
- Minimizing waste during production
- Recycling scrap materials
- Utilizing energy-efficient machines and processes
The Future of High Precision Injection Molding
The future of high precision injection molding looks promising, especially with advancements in technology. Here are some trends shaping the industry:
Smart Manufacturing
Integration of AI and IoT (Internet of Things) will enhance process monitoring and quality control, ensuring that precision remains top-notch.
3D Printing Integration
The combination of 3D printing and injection molding processes may open new avenues for rapid prototyping and small-batch production.
Increased Automation
Automation is set to reduce labor costs and increase efficiency while maintaining the precision that high stakes industries require.
Conclusion
High precision injection molding is not just a manufacturing process; it’s a cornerstone of modern production that supports countless industries. Understanding its benefits, applications, and future potential gives businesses like DeepMould an edge in a competitive market. By leveraging advanced technologies and innovative practices, the future of this sector promises to be precise, efficient, and sustainable.
In a world that demands quality and efficiency, adopting high precision injection molding is no longer a luxury but a necessity for businesses aiming for the next level of manufacturing excellence.